Shipbuilding Case Study Tiger Ceramic Allows a Shipbuilder to Meet Back Gouge Standards While Delivering $20K Savings
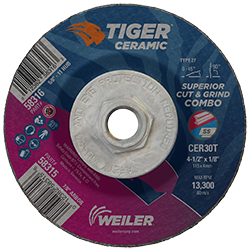
Challenge: Steel Back Gouge Standards Must Be Met for Ship Welding
A United States shipbuilder that specializes in the commercial and defense aluminum vessel market had recently expanded its production to include steel ships. The Welding Engineer charged with leading the expansion faced a challenge that threatened the company’s ability to deliver steel ships to government specifications. According to the Navy Back gouge standard – Mil Standard 1689A, structures that are welded on both sides must be back gouged to sound metal to ensure full penetration of a weld. In this process, back gouging on aluminum is done with carbide blades, however, they are not an effective option on steel. Having no standard operating procedures in place or previous experience testing abrasives the Welding Engineer needed to find an abrasive product that worked on steel. Without a solution, they would not be able to fulfill their current contracts and run the risk of not winning future bids.
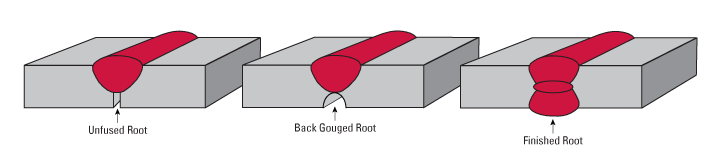
Back gouging procedures are implemented during the shipbuilding process where it is not possible to guarantee the consistency of a weld root. This can occur for several reasons but is primarily where the machining of an accurate weld preparation is not economically viable or practical.
Solution:
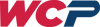
Weiler Application Experts found the current discs used symmetric abrasives grains, which offered a high initial cut-rate but also a rapid reduction of performance.
Weiler Application Experts recommended Tiger Ceramic RFD’s because the grains fracture with less pressure, continuously exposing new sharp edges throughout the life of the disc while also preventing glazing. After testing, operators felt the new disc maintained a high cut-rate much longer.
Result:
Through collaboration, comprehensive testing, and evaluation it was proven that the Tiger Ceramic 1/8 combination wheel was the best solution, delivering an annual savings of $20,000 over the other wheels tested. The Weiler team delivered an SOP to the Welding Engineer for future testing and most importantly solved a production-halting application challenge that threatened current and future business, allowing the shipbuilder to meet customer demands.
“Nobody captures and optimizes grinding costs in shipyard welding, like Weiler.”
- Welding Engineer
$20,000
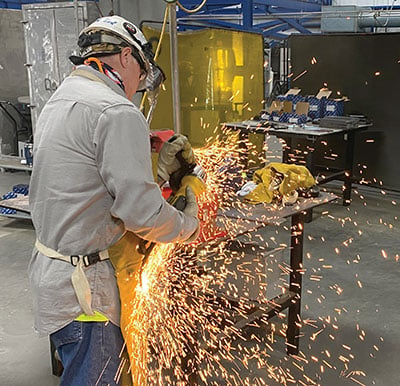
Schedule an On-Site Assessment
The first step to cutting through barriers is to schedule a free on-site assessment where Weiler experts will evaluate how our abrasives can help eliminate inefficiencies, safety issues, and labor shortages in your operation.
Our Approach To Improvement:
- On-Site Assessment
- Test Abrasives
- Measure Results
- Present Documented Cost & Time Savings
Schedule an On-Site Assessment
Don't let inefficiency, safety issues, or labor shortages hold your metal fabrication business back. Contact us today to learn more about how our abrasives for metal can help you achieve a smooth finish, prioritize safety, and address labor shortages with efficient and safe grinding solutions.