Optimal Cleaning in the Foundry Operation
From blending parting lines to grinding burnt sand castings, the foundry cleaning room presents productivity challenges that can often be a bottleneck in the foundry process. Having the right abrasives is critical — that’s why Weiler Abrasives offers a variety of solutions specifically for foundry applications. Our line of abrasives can help you address tough grinding and finishing jobs to decrease cycle times while gaining a quality finish.
We know the job of metal casting isn’t easy and neither is cleaning and finishing, so operators deserve products that are easy and safe to use. Better abrasives mean greater efficiency.
Ceramic Foundry Advantage
Weiler Abrasives is setting the standard for performance in the foundry process with its Tiger® Ceramic abrasives technology. Featuring an ultra-fine micro-structure that self-sharpens, these products provide ultra-fast grinding, high removal rates and a longer wheel life. Weiler Abrasives offers ceramic foundry abrasives in Type 11 cup grinding wheels and Type 27 grinding and combo wheels, as well as cones, plugs and snagging wheels.
Request A ConsultationType 27 Grinding Wheels
Tiger Ceramic has been specifically designed for tough metal foundry applications, offering superior cuts and long life. These depressed center wheels can remove up to 40% more material than competitive zirconia products, resulting in more uptime and fewer abrasives replacements.
Weiler Abrasives has also incorporated an advanced anti-chipping technology to improve operator safety in the foundry operation. It eliminates uneven edge breakage and chipping and reduces the chance of flying debris during grinding. The technology also lengthens wheel life and offers a reliable grinding edge, while a triple fiberglass reinforcement design further increases wheel strength.
Weiler Abrasives also offers the Tiger Type 27 grinding wheel in zirconia and aluminum oxide grain — both performance tiers, with the ceramic setting the highest standard.
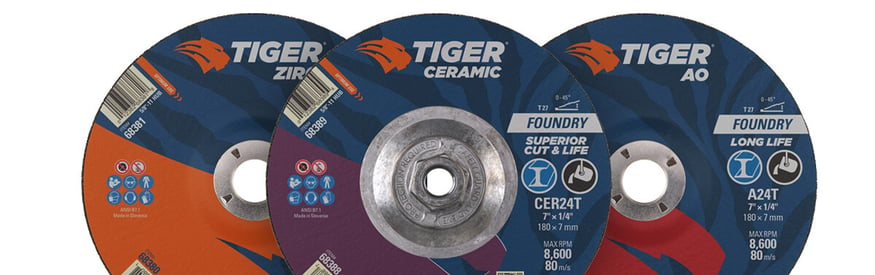
Type 11 Flaring Cup Grinding Wheels
When compared to competitive zirconia cups, Weiler Abrasives industry-exclusive ceramic grain technology allow the Tiger Ceramic cup grinding wheels to cut up to 30% faster. This results in high metal removal and improved productivity in the foundry cleaning room, especially on hard-to-grind materials. A balanced cup design reduces vibration and operator fatigue.
Each cup wheel includes a Weiler Abrasives exclusive safety feature — an anchored hexagon nut that secures the cup in place, locking it to the tool. Operators can have peace of mind when working on the most challenging metal casting foundry jobs, knowing that the cup is secure and resists breakage. This zinc-plated nut also resists oxidation and compared to cups with standard metal backs, offers up to three times higher torque holding strength and withstands double speed burst test ratings.
Tiger cup wheels are also available in zirconia for fast metal removal, silicon carbide for burnt sand castings and alumina oxide grains for cast iron metal foundry applications.
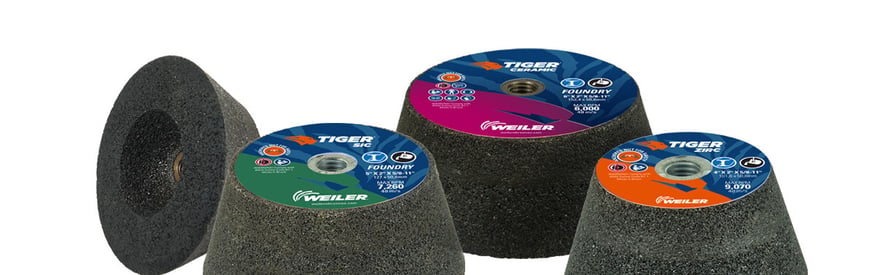
Cones & Plugs
For use with straight grinders, Tiger cones and plugs provide an aggressive cut-rate from start to finish. They are ideal for ID cleaning, hole edge beveling, cleaning castings in hard-to-reach areas. Each cone and plug feature an anchored, heavy-duty steel hex nut to secure the abrasives to the grinder and improve operator safety.
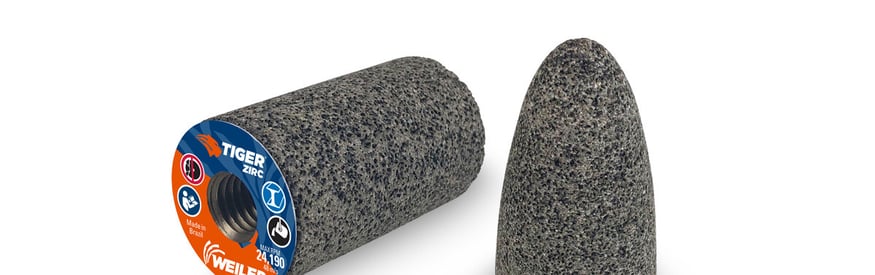
Snagging Wheels
Tiger Type 1 portable snagging wheels for pneumatic straight grinders and high frequency electric straight grinders support heavy stock removal, rough beveling, and snagging. They are available in 3, 6- and 8-inch wheels with double fiberglass reinforcements to increase strength and resist chipping.
Weiler Abrasives offers the cones, plugs and snagging wheels for the foundry cleaning room including Tiger Ceramic, Tiger Zirc and Tiger AO. Each abrasive type and grain provide smooth, vibration-free operation to improve operator comfort and lessen fatigue. An open face design also provides aggressive cut-rate right out of the box.
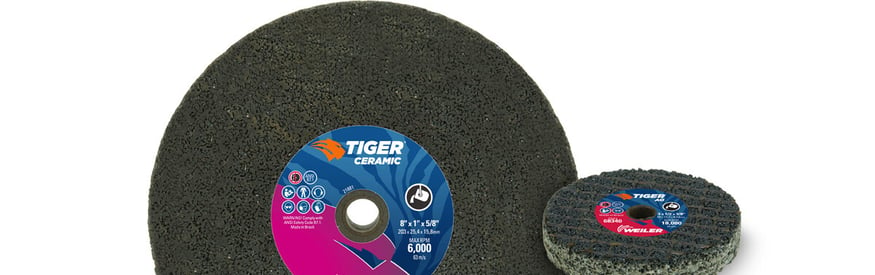
Mounted Points
Ideal for cleaning IDs, complex geometries, hard-to-reach places and more, Tiger Zirc mounted points are available in a variety of shapes. They feature an engineered stem bonding for strength, stability and safety and have a dressed work surface, so operators don’t need to break them in.
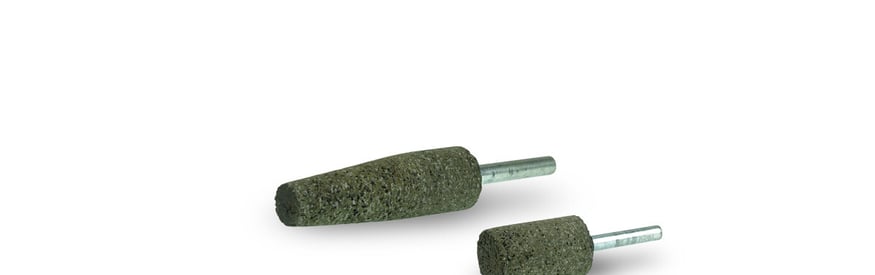
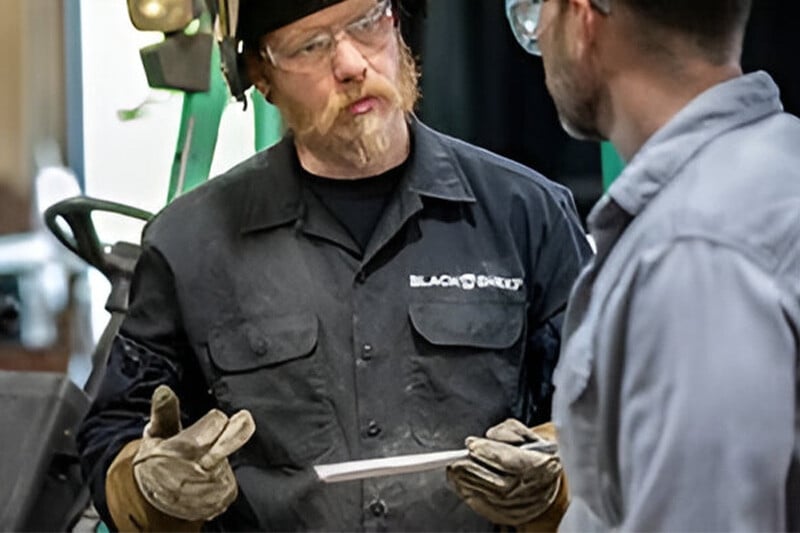
Consumable Productivity Program:
This program allows Weiler Abrasives specialists to collect data on-site, evaluate abrasive use and offer recommendations for abrasives that optimize grinding and improve throughput.

SPOT Safety Training
Weiler Abrasives offers safety training based on SPOT (Speed & Size, Pressure, Orientation, Time) to help operators learn the proper and safe way to use abrasives.
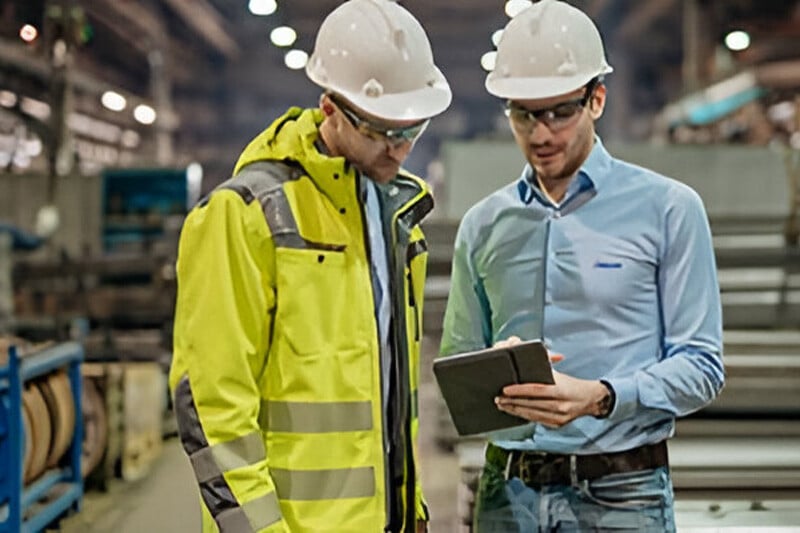
Engineered Products & Custom Solutions
For challenging metal foundry applications, Weiler Abrasives can offer custom-engineered products or evaluations to provide solutions to difficult problems.
Our Commitment
The Weiler Abrasives team is committed to helping foundries like yours eliminate the bottleneck in the grinding process so you can increase production efficiency, meet customer expectations, and improve profitability. Schedule a consultation with an abrasives expert today and let's find your improvements.
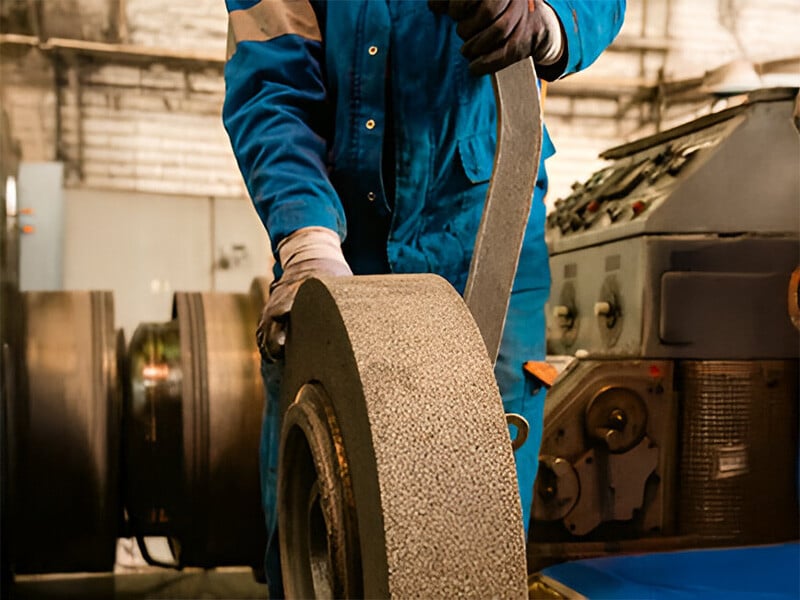
Recognizing Trends of Roll Grinding Operations
Roll grinding is a specialized form of external cylindrical grinding designed for rolls, which are significantly larger than typical grinding parts. These rolls, used in hot or cold rolling mills, require regular maintenance to remove deformations and ensure smooth mill operation.
Roll maintenance has always been a challenge, but with technological advancements, we can now focus on productivity, quality, and cost efficiency. Rolls made from hard-to-grind materials pose a unique challenge, requiring grinding wheels with a special grain mixture and an advanced bonding system to achieve an efficient grinding process with the desired outcome. In roll grinding, operations constantly seek wheels with high G-ratios and material removal rates (MRR) that don't compromise roll integrity or safety.
Helping You Gain a Competitive Advantage
We address these challenges with custom-made products tailored to your needs, optimizing performance. Our abrasive wheels maximize G-ratios and MRR, ensuring quick material removal while protecting roll quality and safety. Our solutions offer desired surface finishes, preventing defects like feed lines, chattering, or burns and cracks.
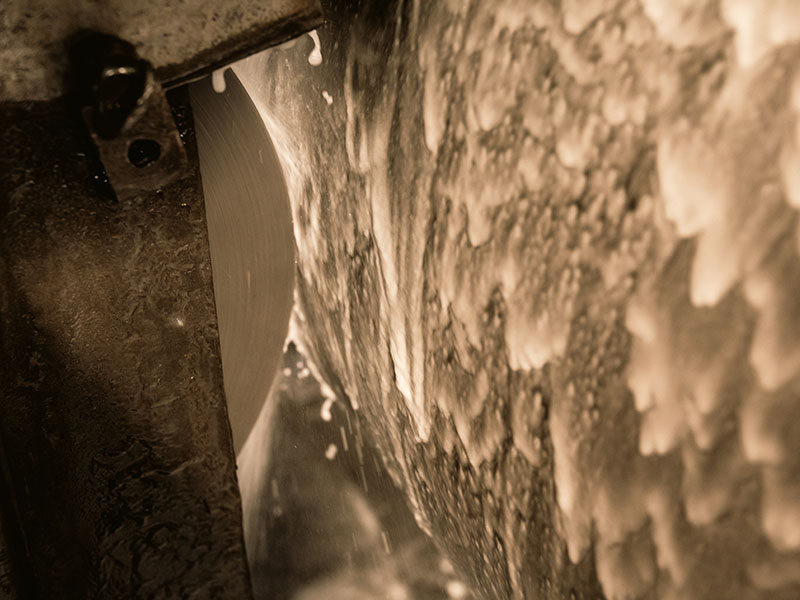
Tailored Solutions
Tailored Solutions
Custom formulations for various roll materials enhance performance and reduce abrasive costs.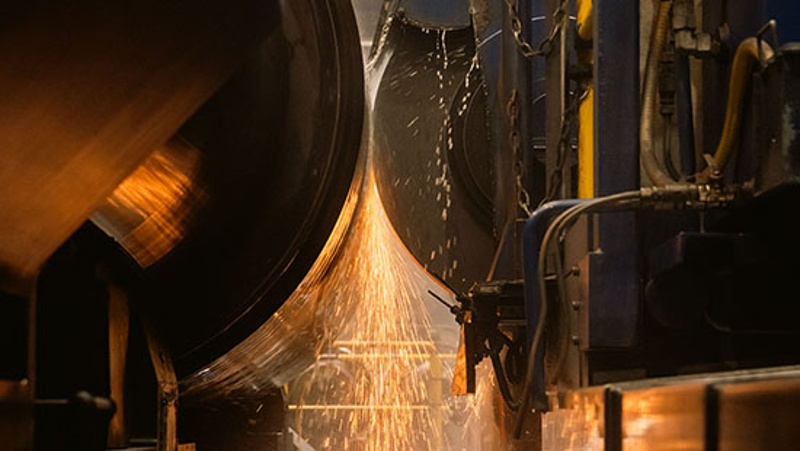
Reduce Vibration
Reduce Vibration
Eliminate surface imperfections, improve roll quality, and extend the life of rolls and equipment.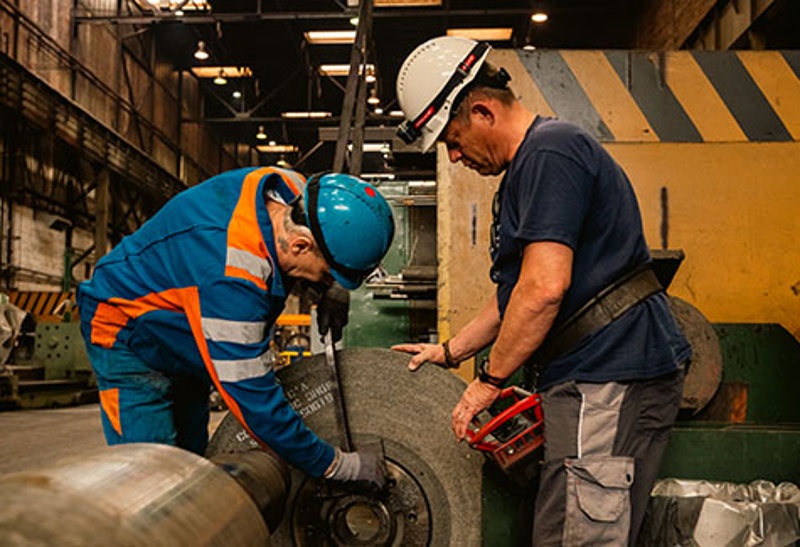
Shorten Cycle Times
Shorten Cycle Times
Enhancing abrasive performance reduces cycle times and minimizes production downtime.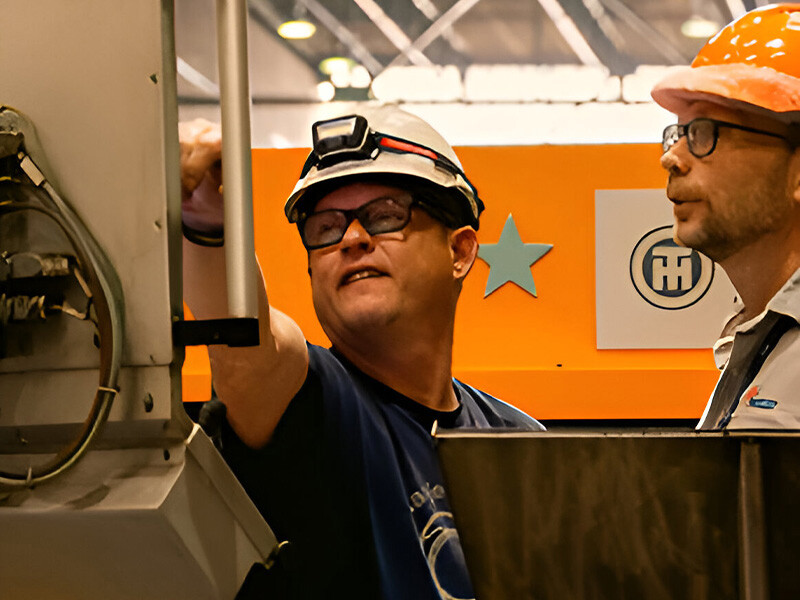
Increase Precision
Increase Precision
Achieve tighter tolerances by eliminating variations and increasing product quality.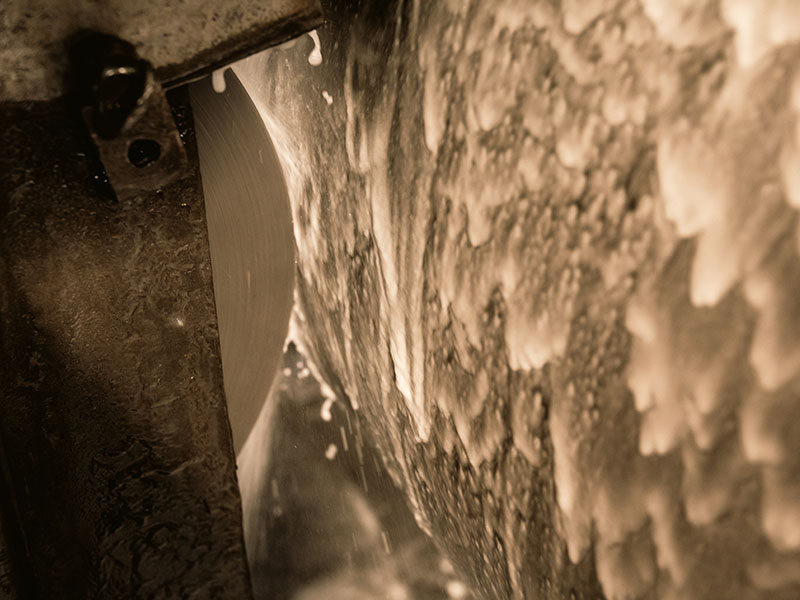
Tailored Solutions
Tailored Solutions
Custom formulations for various roll materials enhance performance and reduce abrasive costs.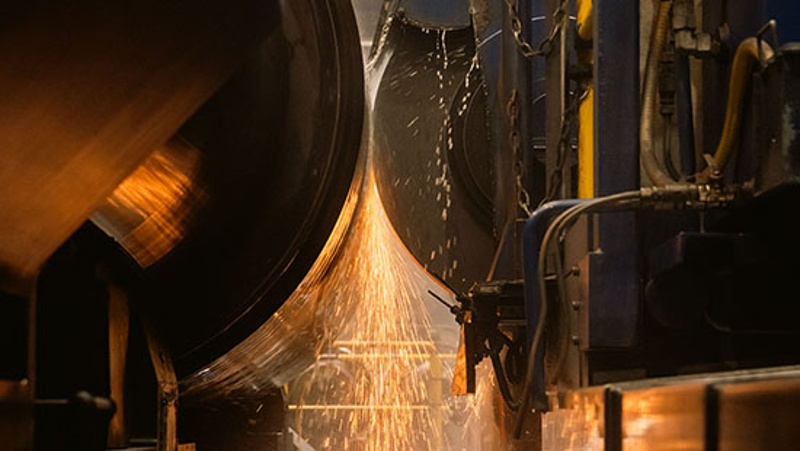
Reduce Vibration
Reduce Vibration
Eliminate surface imperfections, improve roll quality, and extend the life of rolls and equipment.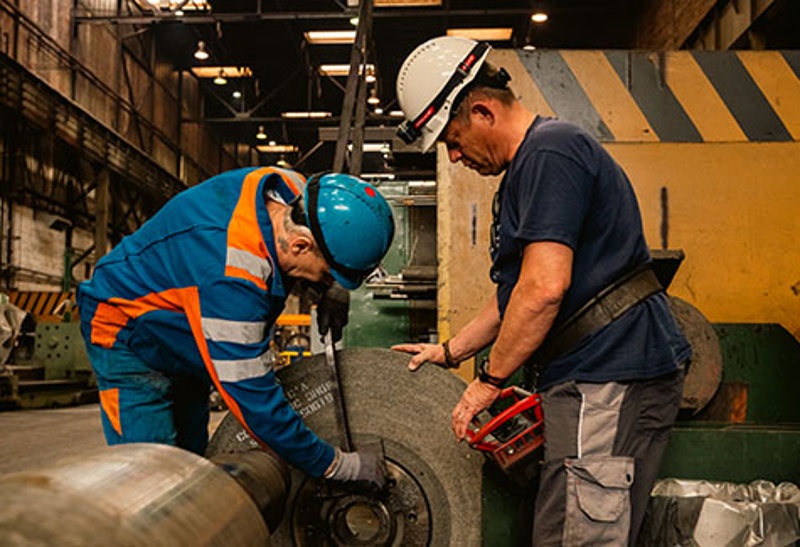
Shorten Cycle Times
Shorten Cycle Times
Enhancing abrasive performance reduces cycle times and minimizes production downtime.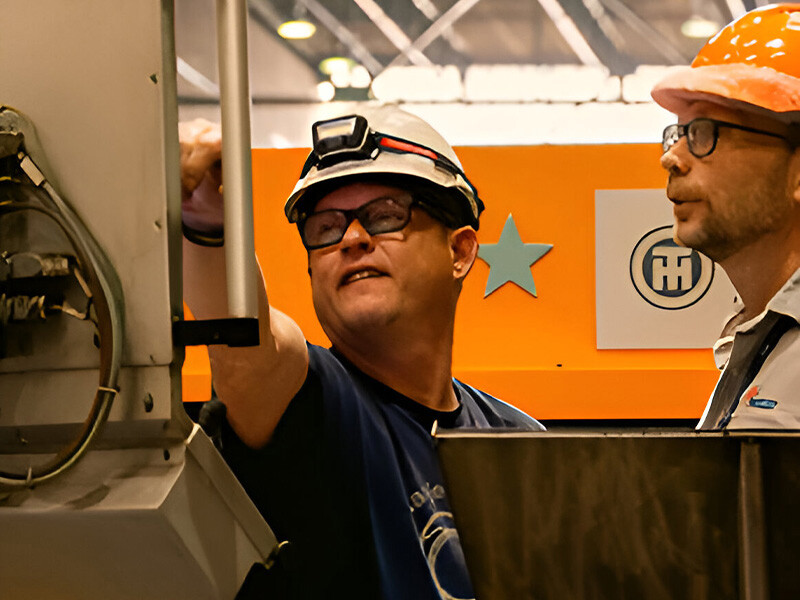
Increase Precision
Increase Precision
Achieve tighter tolerances by eliminating variations and increasing product quality.Weiler Process Solutions: Bringing Process, Expertise, And Partnership Together.
Weiler Process Solutions (WPS) offers tailored solutions to optimize production, reduce costs, and improve productivity in your roll grinding operations.
LEARN ABOUT WPSHot Roll Mill Grinding
Roll Grinding Solutions That Deliver Results
In hot rolling mills, rolls face high pressures and heat, causing deformation. Regular grinding is essential to maintain efficiency, focusing on:
High material removal rates | Short grinding times | High G-ratiosIn hot rolling mills, abrasives with grit sizes from 30 to 46 are recommended. Our custom grinding wheels, available in all standard dimensions and resin-bonded or vitrified versions, feature an advanced self-sharpening effect and comply with EN 12413 and oSa standards. They are ideal for grinding forged and casted rolls, offering increased G-ratios, extended roll life, and reduced production costs, leading to significant productivity improvements.
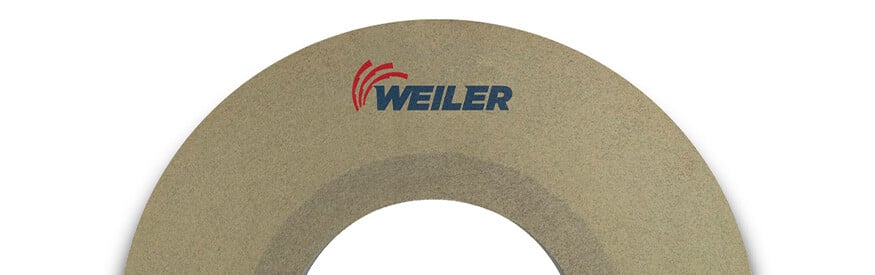
Cold Roll Mill Grinding
In cold rolling mills, precision is critical. The grinding process ensures:
The smoothest possible surface without scratches or mark | Uniform straightness across the roll lengthMinimal material removal to extend roll life | Specific surface roughness for quality assurance
Rolls are ground to precise roughness levels (0.2µm to 0.5µm) using abrasive grit ranging from 46 to 220. Our specialized grinding wheels, available in resin-bonded or vitrified versions, feature an advanced self-sharpening effect and comply with EN 12413 and oSa standards. They ensure consistent edge shape, prevent defects, and extend wheel life. These features result in flawless finishes, reduced production costs, and enhanced productivity, enabling cold mills to operate with unmatched efficiency and product quality.
